OPZV
1.The high-temperature and high-humidity plate solidification process ensures the reasonable composition of the positive plate, making the battery have a good deep cycle life.
2.The grid alloy adopts a multi-element formula to avoid early capacity loss and failure modes such as water loss and drying. It strengthens the bond between the active material and the grid alloy, resulting in strong conductivity and extending the battery life.
3.The battery adopts processes such as polar group formation, dual formation, acid injection in fixed quantities, and consistency testing of internal resistance, voltage, and capacity. This ensures high consistency among batteries used in groups, with a float voltage difference ≤40 mV, initial voltage difference ≤20 mV, and internal resistance difference ≤15%.
4.The application of engineering shell materials, safety valves, and AGM separators ensures a battery reaction efficiency of ≥99% and a safety valve’s opening and closing pressure control accuracy of ±1 Kpa. The thickened shell of 12-16 mm can adapt to different application environments with varying altitudes and temperature/humidity conditions. In harsh conditions such as dryness and low air pressure, the battery experiences minimal water loss, no cracking, and gas expansion, ensuring safe usage.
5.The battery uses a glass fiber absorbent separator and employs low electrolyte technology, resulting in internal gas recombination during use and no acid mist overflow. Therefore, there is no need to add water or check the electrolyte specific gravity throughout the entire usage period, ensuring safety and convenience.

Classification:
Backup Power Supply

Keywords:
OPZV
Detailed description
1.The high-temperature and high-humidity plate solidification process ensures the reasonable composition of the positive plate, making the battery have a good deep cycle life.
2.The grid alloy adopts a multi-element formula to avoid early capacity loss and failure modes such as water loss and drying. It strengthens the bond between the active material and the grid alloy, resulting in strong conductivity and extending the battery life.
3.The battery adopts processes such as polar group formation, dual formation, acid injection in fixed quantities, and consistency testing of internal resistance, voltage, and capacity. This ensures high consistency among batteries used in groups, with a float voltage difference ≤40 mV, initial voltage difference ≤20 mV, and internal resistance difference ≤15%.
4.The application of engineering shell materials, safety valves, and AGM separators ensures a battery reaction efficiency of ≥99% and a safety valve’s opening and closing pressure control accuracy of ±1 Kpa. The thickened shell of 12-16 mm can adapt to different application environments with varying altitudes and temperature/humidity conditions. In harsh conditions such as dryness and low air pressure, the battery experiences minimal water loss, no cracking, and gas expansion, ensuring safe usage.
5.The battery uses a glass fiber absorbent separator and employs low electrolyte technology, resulting in internal gas recombination during use and no acid mist overflow. Therefore, there is no need to add water or check the electrolyte specific gravity throughout the entire usage period, ensuring safety and convenience.
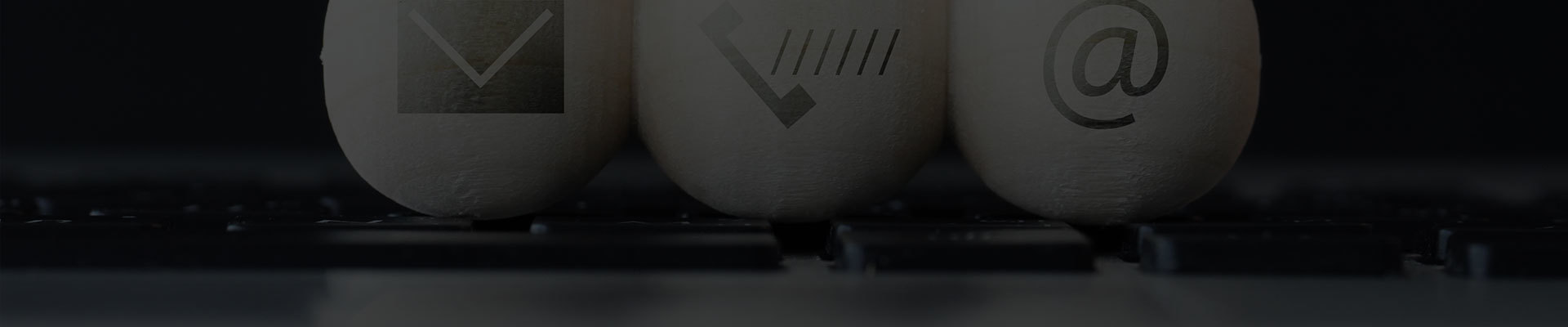
Inquiry